Toyota RAV4 (XA40) 2013-2018 Service Manual: Evap system
Related dtcs
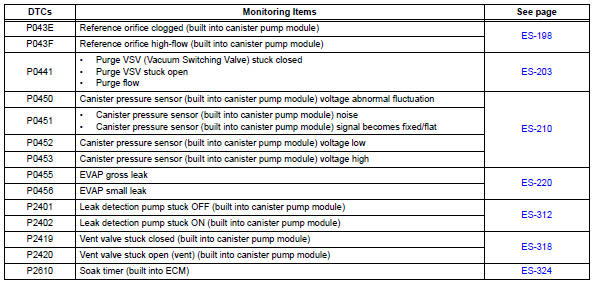
If any evap system dtcs are set, the malfunctioning area can be determined
using the table below.
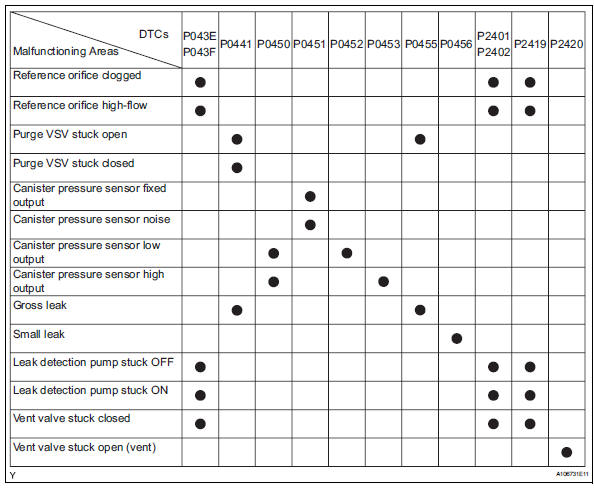
Notice:
If the reference pressure difference between the first and second checks
is greater than the
specification, all the dtcs relating to the reference pressure (p043e, p043f,
p2401, p2402 and
p2419) are stored.
Description
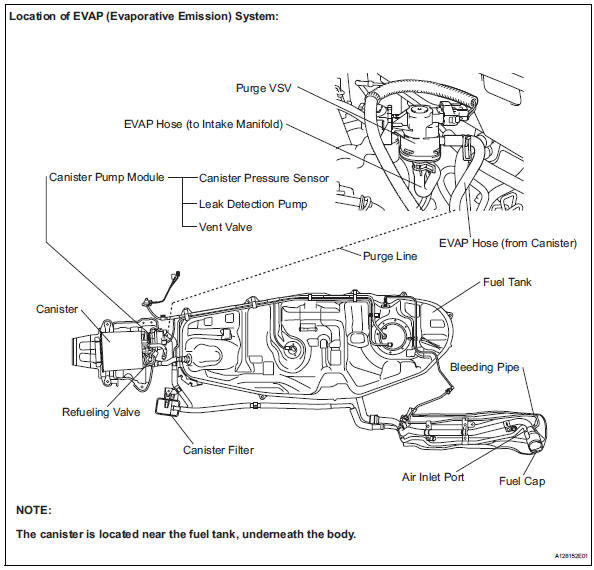
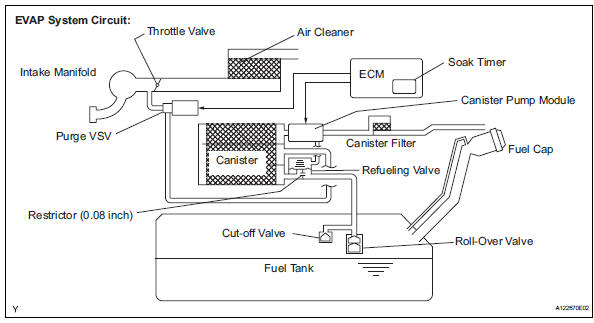
Notice:
In this vehicle's evap system, turning on the vent valve does not seal off
the evap system. To
check for leaks in the evap system, disconnect the air inlet vent hose and apply
pressure from
the atmospheric side of the canister.
While the engine is running, if a predetermined condition (closed-loop, etc.)
Is met, the purge vsv is
opened by the ecm and stored fuel vapors in the canister are purged into the
intake manifold. The ecm
changes the duty cycle ratio of the purge vsv to control purge flow volume.
The purge flow volume is also determined by the intake manifold pressure.
Atmospheric pressure is
allowed into the canister through the vent valve to ensure that the purge flow
is maintained when the
negative pressure (vacuum) is applied to the canister.
The following two monitors run to confirm the appropriate evap system operation.
- Key-off monitor
This monitor checks for evap (evaporative emission) system leaks and canister
pump module
malfunctions. The monitor starts 5 hours* after the ignition switch is turned
off. At least 5 hours are
required for the fuel to cool down to stabilize the evap pressure, thus making
the evap system
monitor more accurate.
The leak detection pump creates negative pressure (vacuum) in the evap system
and the pressure
is measured. Finally, the ecm monitors for leaks from the evap system, and
malfunctions in both the
canister pump module and purge vsv, based on the evap pressure.
Hint:
*: If the engine coolant temperature is not below 35°c (95°f) 5 hours after
the ignition switch is
turned off, the monitor check starts 2 hours later. If it is still not below
35°c (95°f) 7 hours after the
ignition switch is turned off, the monitor check starts 2.5 Hours later.
- Purge flow monitor
The purge flow monitor consists of the two monitors. The 1st monitor is
conducted every time and the
2nd monitor is activated if necessary.
While the engine is running and the purge vsv (vacuum switching valve) is on
(open), the ecm
monitors the purge flow by measuring the evap pressure change. If negative
pressure is not
created, the ecm begins the 2nd monitor.
The vent valve is turned off (open) and the evap pressure is measured. If the
variation in the
pressure is less than 0.5 Kpa-g (3.75 Mmhg-g), the ecm interprets this as the
purge vsv being
stuck closed, and illuminates the mil and sets dtc p0441 (2 trip detection
logic).
Atmospheric pressure check:
in order to ensure reliable malfunction detection, the variation between the
atmospheric pressures, before
and after conduction of the purge flow monitor, is measured by the ecm.
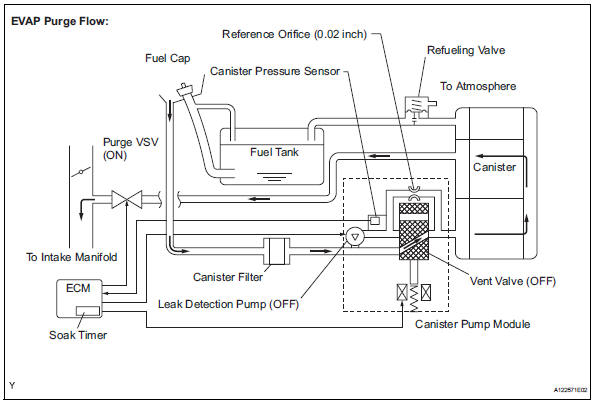
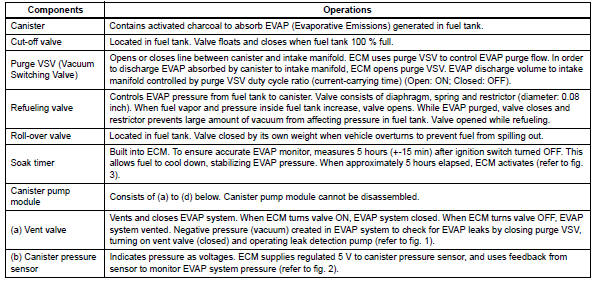

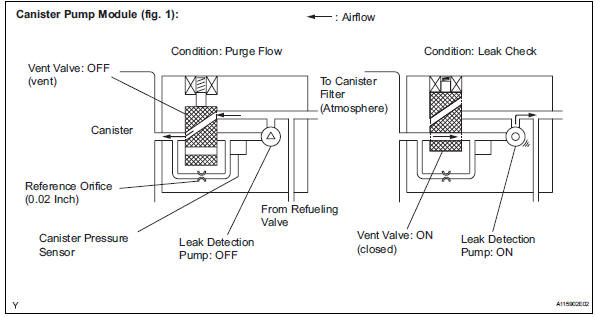
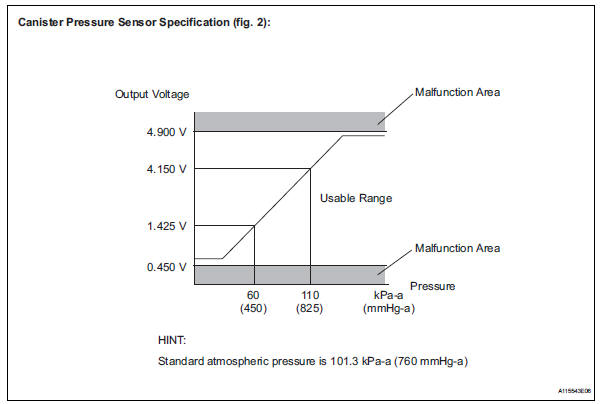
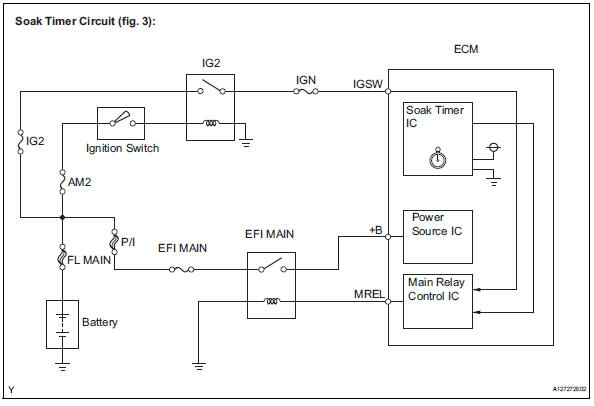
Wiring diagram
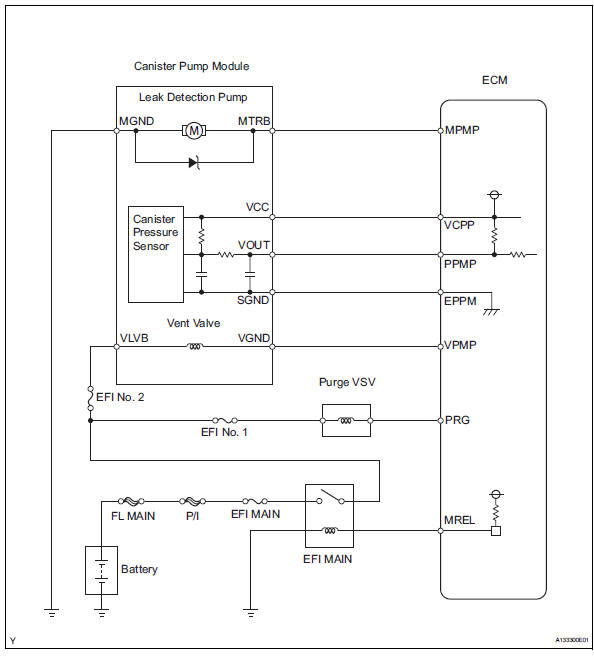
Inspection procedure
Notice:
The intelligent tester is required to conduct the following diagnostic
troubleshooting procedure.
Hint:
- Using intelligent tester monitor results enables the evap (evaporative
emission) system to be
confirmed.
- Read freeze frame data using the intelligent tester. Freeze frame data
records the engine condition
when malfunctions are detected. When troubleshooting, freeze frame data can
help determine if the
vehicle was moving or stationary, if the engine was warmed up or not, if the
air-fuel ratio was lean or
rich, and other data from the time the malfunction occurred.
- Confirm dtc
- Turn the ignition switch off and wait for 10 seconds.
- Turn the ignition switch on.
- Turn the ignition switch off and wait for 10 seconds.
- Connect an intelligent tester to the dlc3.
- Turn the ignition switch on and turn the tester on.
- Confirm dtcs and freeze frame data.
If any evap system dtcs are set, the malfunctioning
area can be determined using the table below.
Notice:
If the reference pressure difference between the first
and second checks is greater than the specification,
all the dtcs relating to the reference pressure
(p043e, p043f, p2401, p2402 and p2419) are stored.
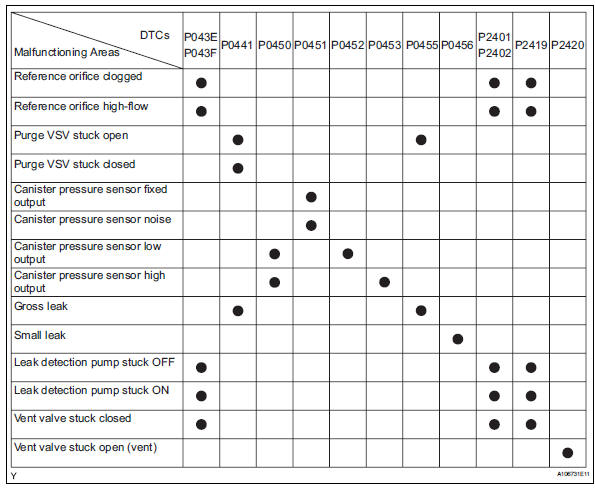
- Perform evap system check (auto operation)
Notice:
- The evap system check (auto operation)
consists of 5 steps performed automatically by the
intelligent tester. It takes a maximum of approximately
18 minutes.
- Do not perform the evap system check when the
fuel tank is more than 90% full because the cut-off
valve may be closed, making the fuel tank leak check
unavailable.
- Do not run the engine during this operation.
- When the temperature of the fuel is 35°c (95°f) or
more, a large amount of vapor forms and any check
results become inaccurate. When performing the
evap system check, keep the temperature below
35°c (95°f).
- Clear dtcs (see page es-35).
- On the tester, select the following menu items:
diagnosis / enhanced obd ii / system check /
evap sys check / auto operation.
- After the evap system check is completed, check
for pending dtcs by selecting the following menu items:
diagnosis / enhanced obd ii / dtc info /
pending codes.
Hint:
If no pending dtcs are displayed, perform the
monitor confirmation (see "diagnostic help"
menu). After this confirmation, check for pending dtcs.
If no dtcs are displayed, the evap system is normal.

- Perform evap system check (manual operation)
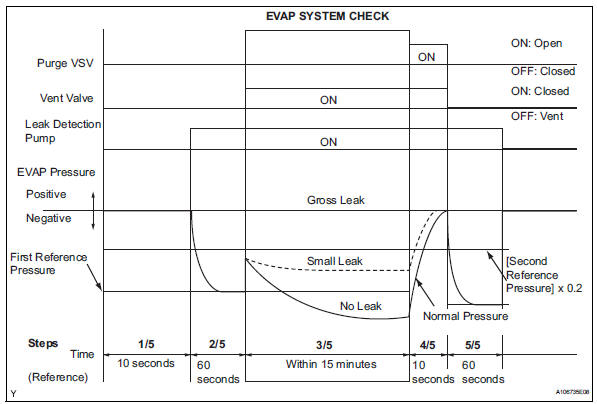
Notice:
- In the evap system check (manual operation),
perform the series of 5 evap system check steps
manually using the intelligent tester.
- Do not perform the evap system check when the
fuel tank is more than 90% full because the cut-off
valve may be closed, making the fuel tank leak check
unavailable.
- Do not run the engine during this operation.
- When the temperature of the fuel is 35°c (95°f) or
more, a large amount of vapor forms and any check
results become inaccurate. When performing the
evap system check, keep the temperature below
35°c (95°f).
- Clear dtcs (see page es-35).
- Select the following menu items: diagnosis /
enhanced obd ii / system check / evap sys
check / manual operation.
- Perform evap system check (step 1/5)
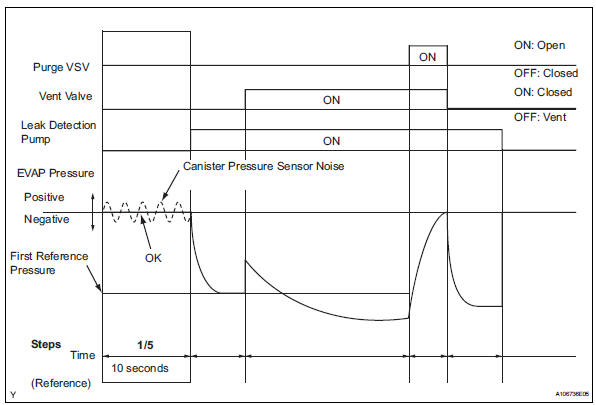
- Check the evap pressure in step 1/5.

*: These dtcs are already present in the ecm when the
vehicle arrives and are confirmed in the "confirm
dtc" procedures above.

- Perform evap system check (step 1/5 to 2/5)
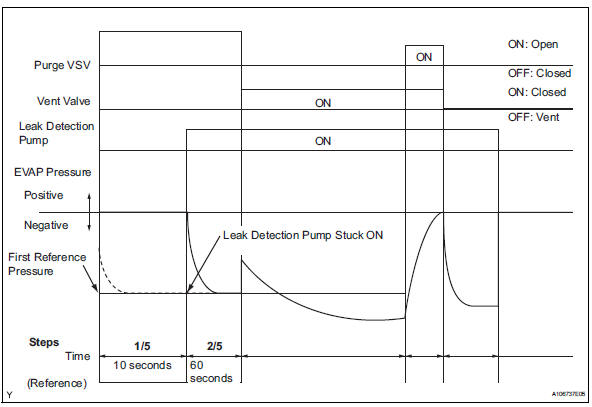
- Check the evap pressure in steps 1/5 and 2/5.

*: These dtcs are already present in the ecm when the
vehicle arrives and are confirmed in the "confirm
dtc" procedures above.
Hint:
The first reference pressure is the value determined in
step 2/5.


- Perform evap system check (step 2/5)
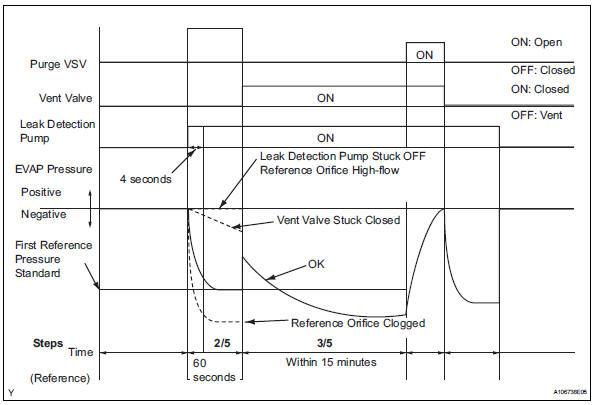
Hint:
Make a note of the pressures checked in steps (a) and (b)
below.
- Check the evap pressure 4 seconds after the leak
detection pump is activated*.
*: The leak detection pump begins to operate as step 1/5
finishes and step 2/5 starts.
- Check the evap pressure again when it has stabilized.
This pressure is the reference pressure.
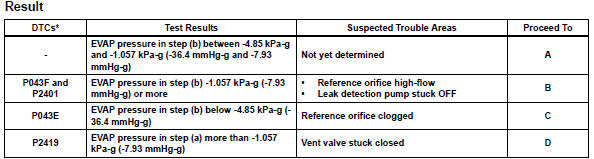
*: These dtcs are already present in the ecm when the
vehicle arrives and are confirmed in the "confirm dtc"
procedures above.
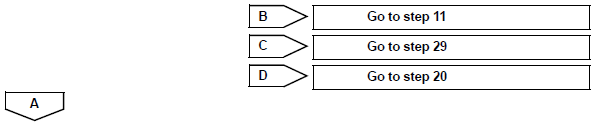
- Perform evap system check (step 2/5 to 3/5)
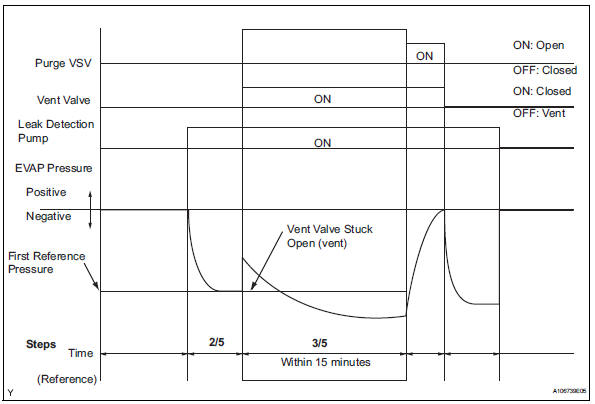
- Check the evap pressure increase in step 3/5.
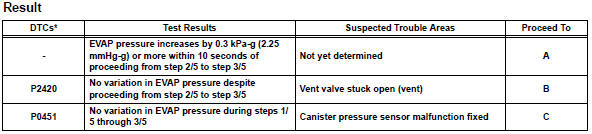
*: These dtcs are already present in the ecm when the
vehicle arrives and are confirmed in the "confirm
dtc" procedures above.


- Perform evap system check (step 3/5)
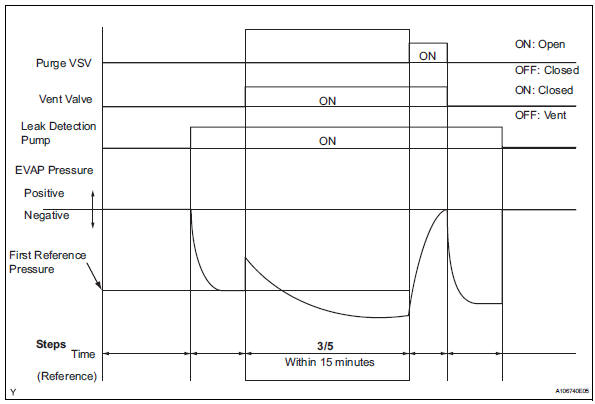
- Wait until the evap pressure change is less than 0.1
Kpa-g (0.75 Mmhg-g) for 30 seconds.
- Measure the evap pressure and record it.
Hint:
A few minutes are required for the evap pressure to
become saturated. When there is little fuel in the fuel
tank, it takes up to 15 minutes.
- Perform evap system check (step 4/5)
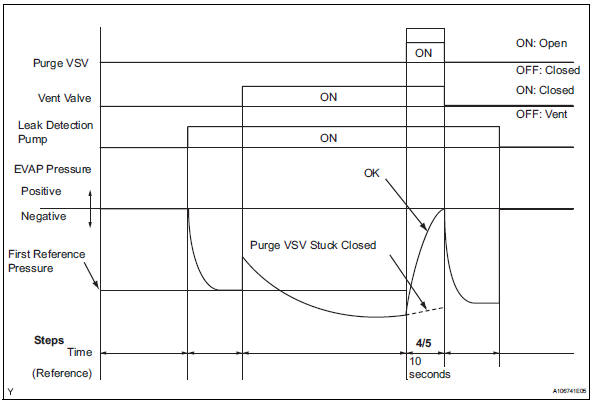
- Check the evap pressure in step 4/5.
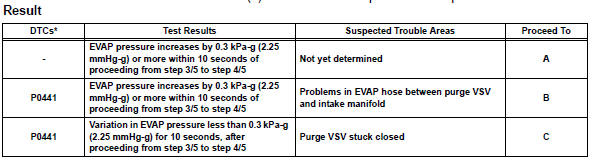
*: These dtcs are already present in the ecm when the
vehicle arrives and are confirmed in the "confirm
dtc" procedures above.

- Perform evap system check (step 5/5)
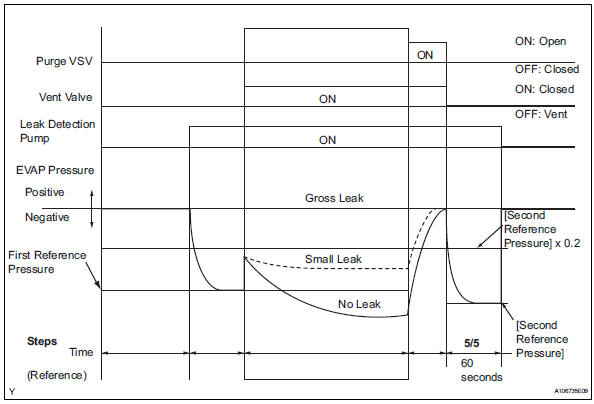
- Check the evap pressure in step 5/5.
- Compare the evap pressure in step 3/5 and the second
reference pressure (step 5/5).
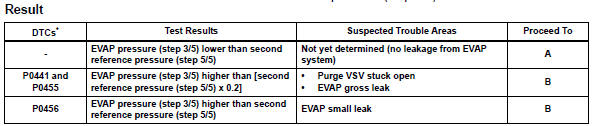
*: These dtcs are already present in the ecm when the
vehicle arrives and are confirmed in the "confirm
dtc" procedures above.

- Perform evap system check (step 3/5)
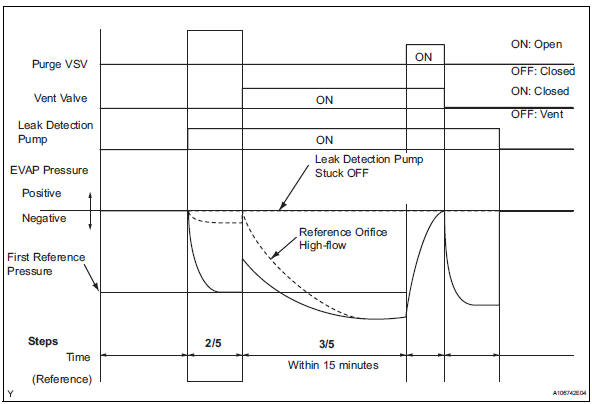
- Check the evap pressure in step 3/5.

*: These dtcs are already present in the ecm when the
vehicle arrives and are confirmed in the "confirm
dtc" procedures above.
Hint:
The first reference pressure is the value determined in
step 2/5.

- Perform active test using intelligent tester (purge vsv)
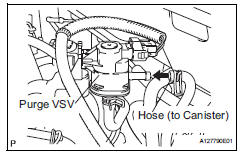
- On the intelligent tester, select the following menu items:
diagnosis / enhanced obd ii / active test /
evap vsv (alone).
- Disconnect the hose (connected to the canister) from the
purge vsv.
- Start the engine.
- Using the tester, turn off the purge vsv (evap vsv:
off).
- Use your finger to confirm that the purge vsv has no
suction.
- Using the tester, turn on the purge vsv (evap vsv:
on).
- Use your finger to confirm that the purge vsv has
suction.
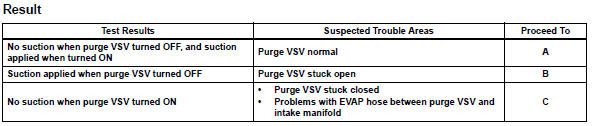
- Reconnect the hose.

- Check fuel cap assembly
- Check that the fuel cap is correctly installed and confirm
the fuel cap meets oem specifications.
- Tighten the fuel cap until a few click sounds are heard.
Hint:
If an evap tester is available, check the fuel cap using
the tester.
- Remove the fuel cap and install it onto a fuel cap
adapter.
- Connect an evap tester pump hose to the adapter,
and pressurize the cap to 3.2 To 3.7 Kpa (24 to 28
mmhg) using an evap tester pump.
- Seal the adapter and wait for 2 minutes.
- Check the pressure. If the pressure is 2 kpa (15
mmhg) or more, the fuel cap is normal.


- Reinstall the fuel cap.
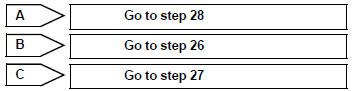
- Inspect duty vacuum switching valve (purge vsv)

- Turn the ignition switch off.
- Disconnect the b2 purge vsv connector.
- Disconnect the hose (connected to the canister) from the
purge vsv.
- Start the engine.
- Use your finger to confirm that the purge vsv has no
suction.

- Reconnect the purge vsv connector.
- Reconnect the hose.

- Check evap hose (purge vsv - intake manifold)
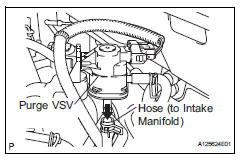
- Disconnect the hose (connected to the intake manifold)
from the purge vsv.
- Start the engine.
- Use your finger to confirm that the hose has suction.

- Reconnect the hose.

- Inspect duty vacuum switching valve (purge vsv)
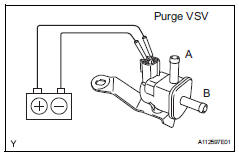
- Remove the purge vsv.
- Apply the battery voltage to the terminals of the purge
vsv.
- Using an air gun, confirm that air flows from port a to port
b.

- Install the purge vsv.


- Check harness and connector (power source of purge vsv)
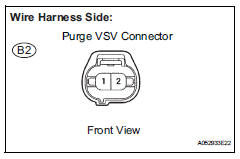
- Disconnect the b2 purge vsv connector.
- Turn the ignition switch on.
- Measure the voltage between terminal 2 of the purge
vsv connector and the body ground.

- Reconnect the purge vsv connector.


- Check harness and connector (purge vsv - ecm)
- Disconnect the b30 ecm connector and the b2 purge
vsv connector.
- Measure the resistance.
Standard resistance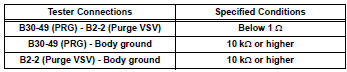
- Reconnect the purge vsv connector.
- Reconnect the ecm connector.
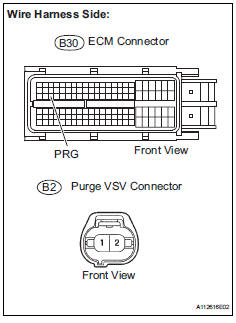

- Inspect canister pump module (power source for vent valve)
- Turn the ignition switch off.
- Disconnect the s3 canister pump module connector.
- Turn the ignition switch on.
- Measure the voltage between vlvb terminal of the
canister pump module connector and the body ground.
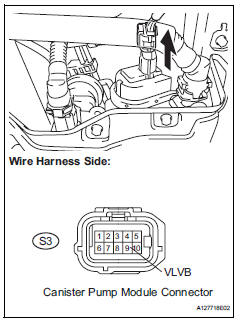
Result

- Reconnect the canister pump module connector.

- Inspect canister pump module (vent valve operation)
- Turn the ignition switch off.
- Disconnect the s3 canister pump module connector.
- Apply the battery voltage to vlvb and vgnd terminals
of the canister pump module.
- Touch the canister pump module to confirm the vent
valve operation.
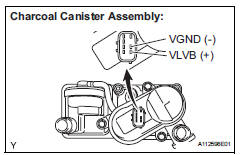


- Reconnect the canister connector.

- Check harness and connector (ecm - canister pump module)
- Disconnect the a9 ecm connector.
- Disconnect the s3 canister pump module connector.
- Measure the resistance between vpmp terminal of the
ecm connector and vgnd terminal of the canister pump
module connector.
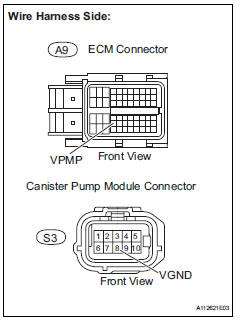

- Reconnect the ecm connector.
- Reconnect the canister pump module connector.

- Perform active test using intelligent tester (vacuum pump (alone))
- Turn the ignition switch off.
- Disconnect the s3 canister pump module connector.
- Turn the ignition switch on.
- On the intelligent tester, select the following menu items:
diagnosis / enhanced obd ii / active test /
vacuum pump.
- Measure the voltage between mtrb terminal 1 of the
canister pump module connector and the body ground
when the leak detection pump is turned on and off
using the tester.
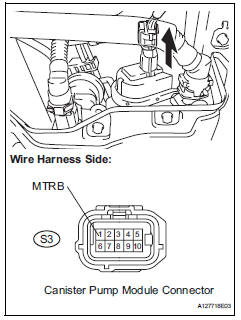
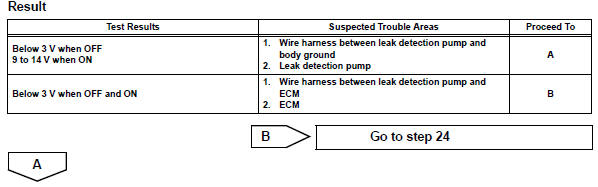
- Check harness and connector (canister pump module - body ground)
- Turn the ignition switch off.
- Disconnect the s3 canister pump module connector.
- Check the resistance between mgnd terminal of the
canister pump module connector and the body ground.
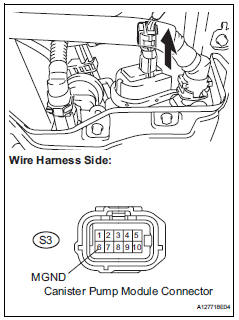

- Reconnect the canister pump module connector.

- Check harness and connector (ecm - canister pump module)
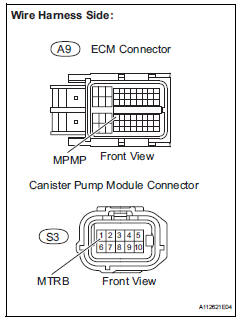
- Turn the ignition switch off.
- Disconnect the s3 canister pump module connector.
- Disconnect the a9 ecm connector.
- Measure the resistance between mpmp terminal of the
ecm connector and mtrb terminal of the canister pump
module connector.

- Reconnect the canister pump module connector.
- Reconnect the ecm connector.

- Inspect intake manifold (evap purge port)
- Stop the engine.
- Disconnect the evap hose from the intake manifold.
- Start the engine.
- Use your finger to confirm that the port of the intake
manifold has suction.

- Reconnect the evap hose.

- Correctly reinstall or replace fuel cap
Hint:
- When reinstalling the fuel cap, tighten it until a few click
sounds are heard.
- When replacing the fuel cap, use a fuel cap that meets
oem specifications, and install it until a few click sounds
are heard.

- Replace fuel cap
Hint:
When installing the fuel cap, tighten it until a few click sounds
are heard.

- Locate evap leak part
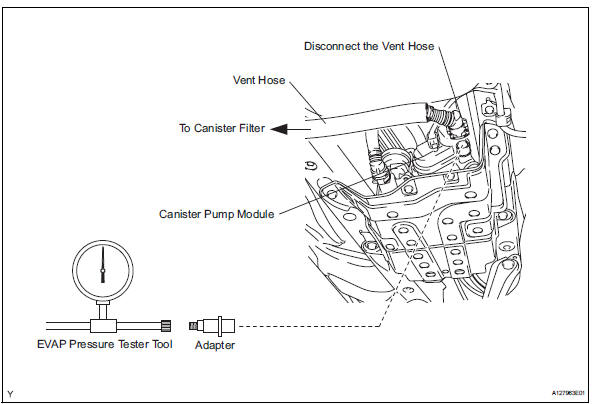
- Disconnect the vent hose.
- Connect the evap pressure tester tool to the canister
pump module with the adapter.
- Pressurize the evap system to 3.2 To 3.7 Kpa (24 to 28
mmhg).
- Apply soapy water to the piping and connecting parts of
the evap system.
- Look for areas where bubbles appear. This indicates the
leak point.
- Repair or replace the leak point.
Hint:
Disconnect the hose between the canister and the fuel
tank from the canister. Block the canister side and
conduct an inspection. In this way, the fuel tank can be
excluded as an area suspected of causing fuel leaks.

- Replace charcoal canister assembly
- Replace the canister assembly (see page ec-10).
Notice:
When replacing the canister, check the canister
pump module interior and related pipes for water,
fuel and other liquids. If liquids are present, check
for disconnections and/or cracks in the following: 1)
the pipe from the air inlet port to the canister pump
module; 2) the canister filter; and 3) the fuel tank
vent hose.
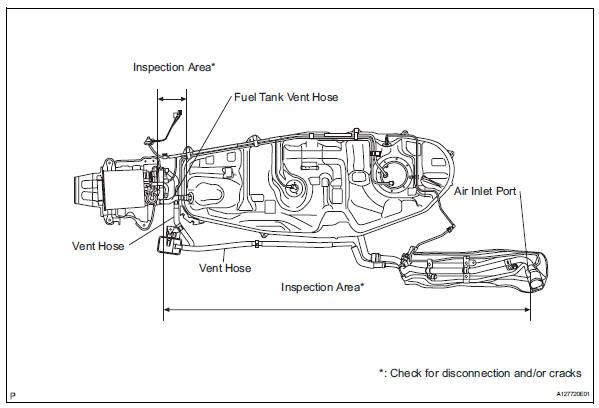

- Replace duty vacuum switching valve (purge vsv)
- Disconnect the connector and the hoses from the purge
vsv.
- Remove the purge vsv.
- Install a new purge vsv.
- Reconnect the connector and hoses.
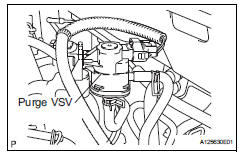

- Repair or replace harness or connector

- Replace evap hose (intake manifold - purge vsv)

- Inspect intake manifold (evap purge port)
- Check that the evap purge port of the intake manifold is
not clogged. If necessary, replace the intake manifold.

- Replace ecm
- Replace the ecm (see page es-429).

- Repair or replace parts and components indicated by output dtcs
- Repair the malfunctioning areas indicated by the dtcs
that had been confirmed when the vehicle was brought
in.

- Perform evap system check (auto operation)
Notice:
- The evap system check (auto operation)
consists of 5 steps performed automatically by the
intelligent tester. It takes a maximum of approximately
18 minutes.
- Do not perform the evap system check when the
fuel tank is more than 90% full because the cut-off
valve may be closed, making the fuel tank leak check
unavailable.
- Do not run the engine in this step.
- When the temperature of the fuel is 35°c (95°f) or
more, a large amount of vapor forms and any check
results become inaccurate. When performing an evap
system check, keep the temperature below 35°c
(95°f).
- Clear dtcs (see page es-35).
- On the intelligent tester, select the following menu items:
diagnosis / enhanced obd ii / system check /
evap sys check / auto operation.
- After the system check is completed, check for
pending dtcs by selecting the following menu items:
diagnosis / enhanced obd ii / dtc info /
pending codes.
Hint:
If no pending dtcs are found, the repair has been
successfully completed.

Completed
Confirmation driving pattern
Hint:
After a repair, check monitor status by performing the key-off monitor
confirmation and purge flow
monitor confirmation described below.
- Key-off monitor confirmation
- Preconditions
The monitor will not run unless:
- The vehicle has been driven for 10 minutes or more (in a city area or on
a freeway)
- The fuel tank is less than 90 % full
- The altitude is less than 8,000 ft (2,400 m)
- The engine coolant temperature (ect) is between 4.4°C and 35°c (40°f and
95°f)
- The intake air temperature (iat) is between 4.4°C and 35°c (40°f and
95°f)
- The vehicle remains stationary (the vehicle speed is 0 km/h [0 mph])
- Monitor conditions
- Allow the engine to idle for at least 5 minutes.
- Turn the ignition switch off and wait for 6 hours (8 or 10.5 Hours).
Hint:
Do not start the engine until checking monitor status. If the engine is
started, the steps
described above must be repeated.
- Monitor status
- Connect the intelligent tester to the dlc3.
- Turn the ignition switch on and turn the tester on.
- Select the following menu items: diagnosis / enhanced obd ii / monitor
status.
- Check the monitor status displayed on the tester.
Hint:
If incmp is displayed, the monitor is not complete. Make sure that the
preconditions have
been met, and perform the monitor conditions again.
- Purge flow monitor confirmation (p0441)
Hint:
Perform this monitor confirmation after the key-off monitor confirmation
shows compl (complete).
- Preconditions
The monitor will not run unless:
- The vehicle has been driven for 10 minutes or more (in a city area or on
a freeway)
- The ect is between 4.4°C and 35°c (40°f and 95°f)
- The iat is between 4.4°C and 35°c (40°f and 95°f)
- Monitor conditions
- Release the pressure from the fuel tank by removing and reinstalling the
fuel cap.
- Warm the engine up until the ect reaches more than 75°c (167°f).
- Increase the engine speed to 3,000 rpm once.
- Allow the engine to idle and turn a/c on for 1 minute.
- Monitor status
- Turn the ignition switch off (if on or the engine is running).
- Connect the intelligent tester to the dlc3.
- Turn the ignition switch on and turn the tester on.
- Select the following menu items: diagnosis / enhanced obd ii / monitor
status.
- Check the monitor status displayed on the tester.
Hint:
If incmp is displayed, the monitor is not complete. Make sure that the
preconditions have
been met, and perform the monitor conditions again.
Monitor result
Refer to checking monitor status (see page es-17).
Hint:
Sensor 1 refers to the sensor mounted in front of the three-way catalytic
converter (twc) and located
near the engine assembly.
Description
Refer to dtc p2195 (see page es-292).
M ...
Description
When the ignition switch is turned on, the battery voltage is applied to the
igsw of the ecm. The output
signal from the mrel terminal of the ecm causes a current to flow to the coil, ...
Other materials:
Reassembly
Install generator rotor assembly
Install the washer onto the generator rectifier end
frame.
Install the generator rotor onto the generator
rectifier end frame.
Using a 32 mm socket wrench and press, slowly
push the generator drive end frame onto the
generator ...
Disposal
Hint:
When scrapping a vehicle equipped with an srs or disposing
of the front passenger side knee airbag, be sure to deploy the
airbag first in accordance with the procedure described
below. If any abnormality occurs with the airbag deployment,
contact the service dept. Of toyota motor sales,
...
Diagnostic trouble code chart
Hint:
If no abnormality is found when inspecting parts, check the
skid control ecu and check for poor contact at the ground
points.
If a dtc is displayed during the dtc check, check the
circuit for the dtc listed in the table below. For details of
each dtc, refer to the page indicated. ...