Toyota RAV4 (XA40) 2013-2018 Service Manual: Disassembly
- Remove idler pulley (see page em-23)
- Remove oil dipstick
- Remove oil dipstick guide (see page em-57)
- Remove manifold stay (see page em-57)
- Remove no. 2 Manifold stay (see page em-58)
- Remove no. 1 Exhaust manifold heat
insulator (see page em-58)
- Remove exhaust manifold converter subassembly
(see page em-58)
- Remove water inlet (see page co-15)
- Remove thermostat
- Remove no. 1 Water by-pass pipe
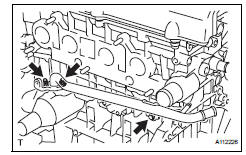
- Remove the bolt, 2 nuts, pipe and gasket.
- Remove no. 3 Water by-pass pipe
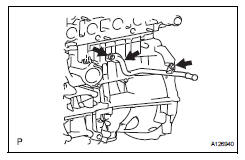
- Remove the bolt, 2 nuts, pipe and gasket.
- Remove v-ribbed belt tensioner assembly
(see page em-26)
- Remove camshaft timing oil control valve
assembly (see page es-395)
- Remove knock sensor (see page es-420)
- Remove radio setting condenser (see page
em-63)
- Remove oil pressure switch assembly (see
page em-63)
- Remove engine coolant temperature
sensor (see page em-63)
- Remove camshaft position sensor (see page
em-64)
- Remove ignition coil assembly (see page ig-9)
- Remove spark plug
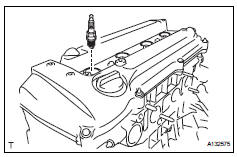
- Remove oil filler cap sub-assembly
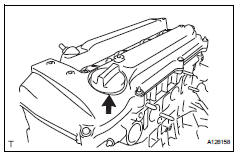
- Remove oil filler cap gasket
- Remove ventilation valve sub-assembly
(see page ec-18)
- Remove cylinder head cover sub-assembly (see
page em-24)
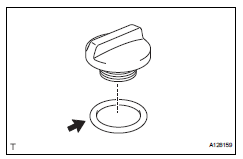
- Remove cylinder head cover gasket
- Remove oil filter sub-assembly (see page lu-
4)
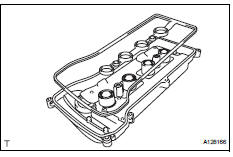
- Remove oil filter union
- Using a 12 mm hexagon wrench, remove the oil
filter union.
- Remove crankshaft position sensor (see page
es-402)
- Remove water pump pulley (see page co-11)
- Remove water pump assembly (see page co- 11)
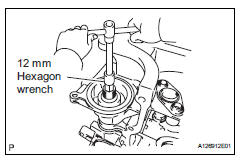
- Remove oil pan drain plug
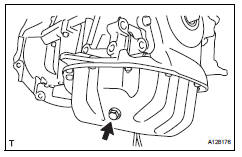
- Remove the oil pan drain plug and gasket.
- Remove oil pan sub-assembly (see page em-
24)
- Remove crankshaft pulley (see page em-25)
- Remove no. 1 Chain tensioner assembly (see
page em-26)
- Remove timing chain cover sub-assembly
(see page em-26)
- Remove no. 1 Crankshaft position sensor plate
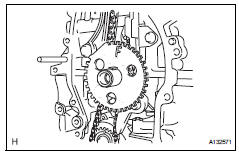
- Remove timing chain guide (see page em-28)
- Remove chain tensioner slipper (see page
em-28)
- Remove no. 1 Chain vibration damper (see
page em-28)
- Remove chain sub-assembly
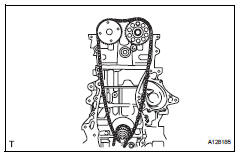
- Remove crankshaft timing sprocket
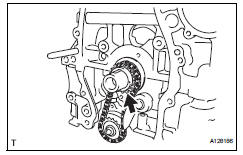
- Remove no. 2 Chain sub-assembly (see page
em-29)
- Remove oil pump drive gear
- Remove oil pump assembly (see page lu-12)
- Remove camshaft
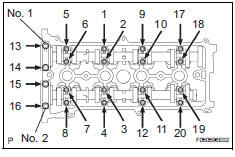
- Using several steps, uniformly loosen and remove
the 20 bearing cap bolts in the sequence shown in
the illustration.
- Remove the 10 bearing caps, then remove the
camshaft and no. 2 Camshaft.
- Remove cylinder head sub-assembly (see
page em-62)
- Remove cylinder head gasket
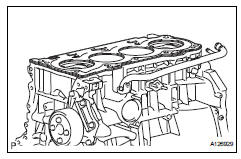
- Remove cylinder block water jacket spacer
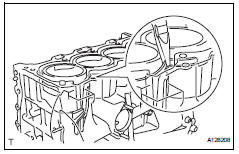
- Using needle-nose pliers, remove the cylinder block
water jacket spacer from the water jacket.
Notice:
Before turning the cylinder block upside down,
make sure that the water jacket spacer is
removed, as it will fall out.
- Remove cylinder block water drain cock
sub-assembly

- Remove oil control valve filter
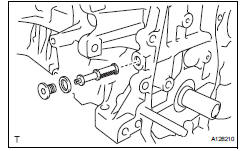
- Using a 6 mm socket hexagon wrench, remove the
plug and gasket.
- Remove the oil control valve filter.
- Inspect balance shaft thrust clearance
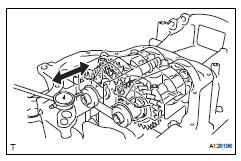
- Using a dial indicator, measure the thrust clearance
while moving the balance shaft back and forth.
Standard thrust clearance:
0.05 To 0.09 Mm (0.0020 To 0.0035 In.)
Maximum thrust clearance:
0.09 Mm (0.0035 In.)
If the thrust clearance is greater than the maximum,
replace the balance shaft housing and bearings. If
necessary, replace the balance shaft.
- Inspect balance shaft oil clearance
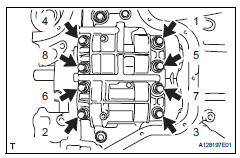
- Using several steps, uniformly loosen and remove
the 8 bolts in the sequence shown in the illustration.
- Remove the balance shaft housing from the
crankcase.
Hint:
Keep the lower bearing and balance shaft housing
together.
- Lift out the no. 1 And no. 2 Balance shafts.
Hint:
Keep the upper bearing with the crankcase.
- Clean each bearing and journal.
- Check each bearing and journal for pitting and
scratches.
If a bearing or journal is damaged, replace the
bearings. If necessary, replace the balance shaft.
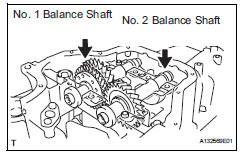
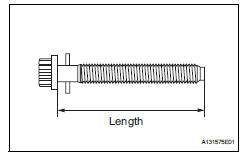
- Inspect the balance shaft housing bolt.
- Using a vernier caliper, measure the length of
the bolts from the seat to the end.
Standard bolt length:
58.3 To 59.7 Mm (2.295 To 2.350 In.)
Maximum bolt length:
60.3 Mm (2.374 In.)
If the bolt length is greater than the maximum,
replace the balance shaft bolt.
- Place the no. 1 And no. 2 Balance shafts onto the
crankcase.
- Lay a strip of plastigage across each journal.
- Install the balance shaft housing.
- Apply a light coat of engine oil on the threads and
under the heads of the bolts.
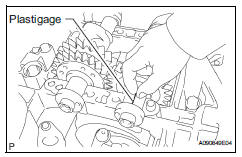
- Using several steps, uniformly install and tighten the
8 bolts in the sequence shown in the illustration.
Torque: 21.6 N*m (220 kgf*cm, 16 ft.*Lbf)
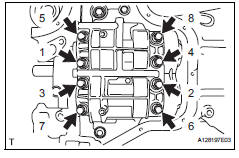
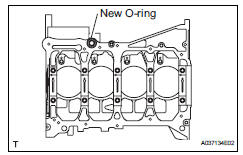
- Mark the front of the bolts with paint.
- Retighten the bolts 90° as shown in the illustration.
- Check that the paint mark is now at a 90° angle to
the front.
- Remove the balance shaft housing from the
crankcase.
- Measure the plastigage at its widest point.
Standard oil clearance:
0.004 To 0.049 Mm (0.0002 To 0.0019 In.)
Maximum oil clearance:
0.049 Mm (0.0019 In.)
Notice:
Remove the plastigage completely after the
measurement.
If the oil clearance is greater than the maximum,
replace the bearing. If necessary, replace the
balance shaft.
Hint:
If replacing a bearing, select a new one with the
same number.
Standard balance shaft housing journal bore
diameter 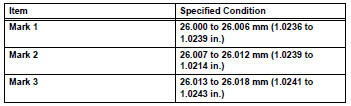
Standard balance shaft journal diameter:
22.985 To 23.000 Mm (0.9049 To 0.9055 In.)
Standard bearing center wall thickness
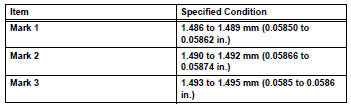
- Remove balance shaft
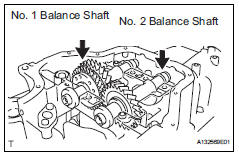
- Remove no. 1 Balance shaft bearing
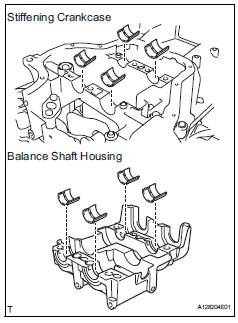
- Remove engine rear oil seal
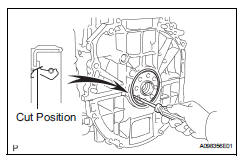
- Using a knife, cut off the lip of the oil seal.
- Using a screwdriver with its tip wrapped with tape,
pry out the oil seal.
Notice:
After removing, check the crankshaft for
damage. If damaged, smooth the surface with
400-grit sandpaper.
- Remove stiffening crankcase assembly
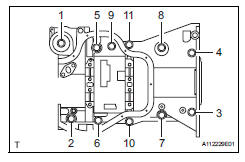
- Using several steps, uniformly loosen and remove
the 11 bolts in the sequence shown in the
illustration.
- Remove the crankcase by prying the portions
between the crankcase and cylinder block.
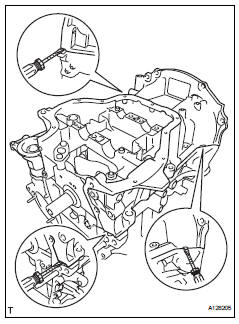
Notice:
Be careful not to damage the contact surfaces of
the crankcase and cylinder bock.
- Remove the o-ring from the cylinder block.
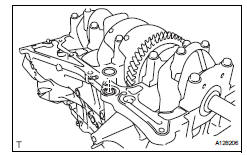
- Inspect connecting rod thrust clearance
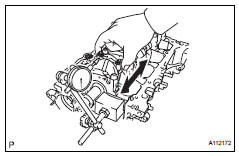
- Using a dial indicator, measure the thrust clearance
while moving the connecting rod back and forth.
Standard thrust clearance:
0.160 To 0.362 Mm (0.0063 To 0.0143 In.)
Maximum thrust clearance:
0.362 Mm (0.0143 In.)
If the thrust clearance is greater than the maximum,
replace the connecting rod. If necessary, replace
the crankshaft.
- Inspect connecting rod oil clearance
Notice:
Do not turn the crankshaft during the measurement.
- Using marking paint, write the matched cylinder
number on each connecting rod and cap.
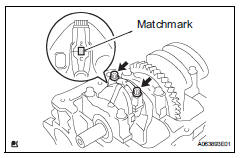
Hint:
The matchmarks in the connecting rods and caps
are for ensuring correct reassembly.
- Using a 12 mm socket wrench, remove the 2 bolts
and connecting rod cap.
- Clean the crank pin and bearing.
- Check the crank pin and bearing for pitting and
scratches.
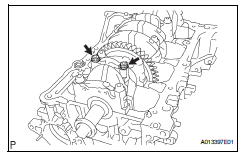
- Lay a strip of plastigage on the crank pin.
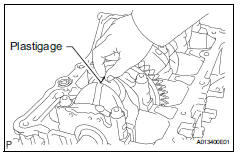
- Check that the front mark of the connecting rod cap
is facing in the correct direction.
- Apply a light coat of engine oil to the threads and
under the heads of the connecting rod bolts.
- Using a 12 mm socket wrench, tighten the bolts in
several passes to the specified torque.
Torque: 24.5 N*m (250 kgf*cm, 18 ft.*Lbf)
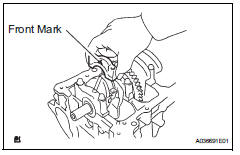
- Mark the front of the connecting rod bolts with paint.
- Retighten the cap bolts 90° as shown in the
illustration.
- Check that the crankshaft turns smoothly.
- Using a 12 mm socket wrench, remove the 2 bolts
and connecting rod cap.
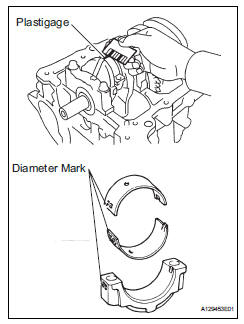
- Measure the plastigage at its widest point.
Standard oil clearance:
0.024 To 0.048 Mm (0.0009 To 0.0019 In.)
Maximum oil clearance:
0.08 Mm (0.0032 In.)
Notice:
Remove the plastigage completely after the
measurement.
If the oil clearance is greater than the maximum,
replace the connecting rod bearing. If necessary,
grind or replace the crankshaft.
Hint:
If replacing a bearing, select a new one with the
same number as marked on the connecting rod.
There are 3 sizes of standard bearings, marked "1",
"2" and "3" accordingly.
Standard connecting rod large end bore
diameter 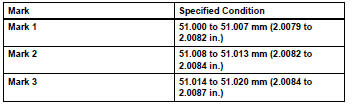
Standard connecting rod bearing thickness
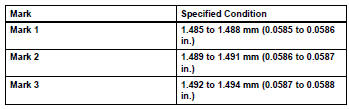
Standard crankshaft pin diameter:
47.990 To 48.000 (1.8894 To 1.8898 In.)
- Remove piston with connecting rod
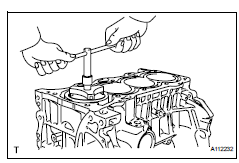
- Using a ridge reamer, remove all the carbon from
the top of the cylinder.
- Push the piston, connecting rod assembly and
upper bearing through the top of the cylinder block.
Hint:
- Keep the bearing, connecting rod and cap
together.
- Arrange the piston and connecting rod
assemblies in the correct order.
- Remove connecting rod bearing
- Remove piston ring set
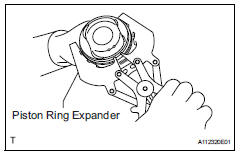
- Using a piston ring expander, remove the 2
compression rings.
- Remove the oil ring and expander by hand.
- Remove piston pin hole snap ring
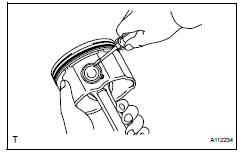
- Using a small screwdriver, pry out the 2 snap rings.
- Remove piston
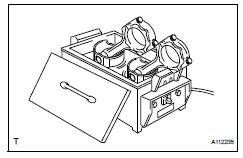
- Gradually heat the piston up to 80 to 90°c (176 to
194°f).
- Using a plastic-faced hammer and brass bar, lightly
tap out the piston pin, then remove the connecting
rod.
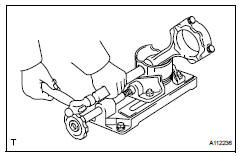
Hint:
- The piston and pin are a matched set.
- Arrange the piston, pin, ring, connecting rod and
bearings in the correct order.
- Inspect crankshaft thrust clearance
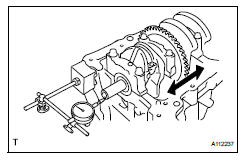
- Using a dial indicator, measure the thrust clearance
while prying the crankshaft back and forth with a
screwdriver.
Standard thrust clearance:
0.04 To 0.24 Mm (0.0016 To 0.0095 In.)
Maximum thrust clearance:
0.30 Mm (0.012 In.)
If the thrust clearance is greater than the maximum,
replace the thrust washers as a set.
Hint:
The thrust washer thickness is 1.93 To 1.98 Mm
(0.0760 To 0.0780 In.).
- Inspect crankshaft oil clearance
Notice:
Do not turn the crankshaft during the measurement.
- Using several steps, uniformly loosen and remove
the 10 bearing cap bolts in the sequence shown in
the illustration.
- Remove the 5 bearing caps from the cylinder block.
Hint:
- Keep the no. 2 Crankshaft bearings and
crankshaft bearing caps together.
- Arrange the bearing caps in correct order.
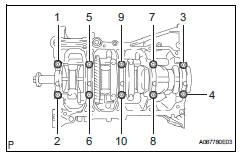
- Remove the crankshaft
Hint:
Keep the crankshaft bearings and crankshaft thrust
washer uppers together with the cylinder block.
- Clean each main journal and bearing.
- Check each main journal and bearing for pitting and
scratches.
- If the journal or bearing is damaged, replace the
bearings.
- If necessary, replace the crankshaft.
- Place the crankshaft onto the cylinder block.
- Lay a strip of plastigage across each journal.
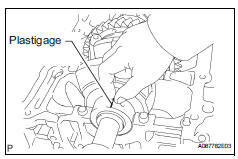
- Examine the front marks and numbers, and install
the bearing caps onto the cylinder block in the order
shown in the illustration.
- Apply a light coat of engine oil to the threads and
under the heads of the crankshaft bearing cap set
bolts.
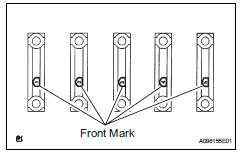
- Using several steps, uniformly install and tighten the
10 bearing cap bolts in the sequence shown in the
illustration.
Torque: 40 n*m (408 kgf*cm, 30 ft.*Lbf)
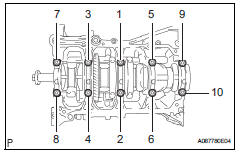
- Mark the front of the bearing cap bolts with paint.
- Retighten the 10 bearing cap bolts by 90°.
- Check that the paint marks are at a 90° angle to the
front.
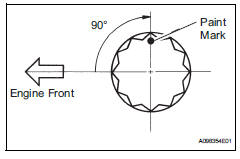
- Remove the crankshaft bearing caps.
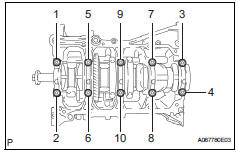
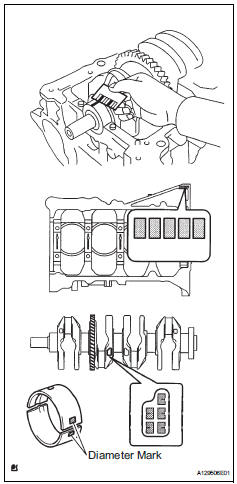
- Measure the plastigage at its widest point.
Standard oil clearance:
0.008 To 0.024 Mm (0.0003 To 0.0010 In.)
Maximum oil clearance:
0.050 Mm (0.0020 In.)
Notice:
Remove the plastigage completely after the
measurement.
If the oil clearance is greater than the maximum,
replace the crankshaft bearing. If necessary,
replace the crankshaft.
Hint:
If replacing a bearing, select a new one with the
same number. If the number of the bearing cannot
be determined, calculate the correct bearing
number by adding together the numbers imprinted
on the cylinder block and crankshaft. Then select a
new bearing with the calculated number. There are
4 sizes of standard bearings, marked "1", "2", "3"
and "4" accordingly.

Example
- Imprinted number on the cylinder block is 3.
- Imprinted number on the crankshaft is 4.
3 + 4 = 7
Select the bearing marked "3".
Standard cylinder block journal bore diameter
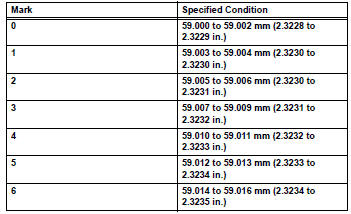
Standard crankshaft journal diameter

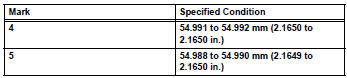
Standard bearing center wall thickness

- Remove crankshaft
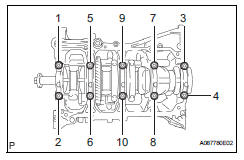
- Using several steps, uniformly loosen and remove
the 10 bearing cap bolts in the sequence shown in
the illustration.
- Remove the 5 bearing caps from the cylinder block.
- Remove the crankshaft from the cylinder block.
- Remove crankshaft thrust washer upper
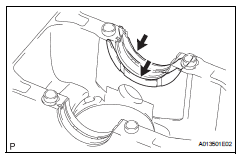
- Remove crankshaft bearing
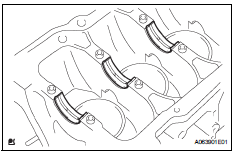
Hint:
Arrange the bearings in the correct order.
- Remove no. 2 Crankshaft bearing
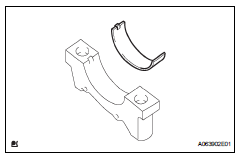
Hint:
Arrange the bearings in the correct order.
- Remove no. 1 Oil nozzle sub-assembly
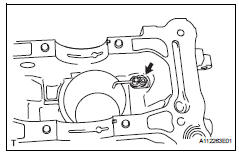
- Remove the 4 bolts and 4 oil nozzles.
Inspect cylinder block for warpage
Using a precision straightedge and feeler gauge,
measure the warpage of the surface that is in
contact with the cylinder head gasket.
Maximum war ...
Other materials:
Removal
Remove radiator support opening cover
Remove front wheel rh
Remove front fender apron rh
Remove front suspension member
reinforcement rh
Remove the 4 bolts and reinforcement rh.
Remove fan and generator v belt
Using sst and 19 mm socket wrench, loosen the vribbed
belt ...
Abs warning light remains on
Description
If any of the following conditions are detected, the abs warning light
remains on:
The ecu connectors are disconnected from the skid control ecu.
There is a malfunction in the skid control ecu internal circuit.
There is an open or short in the wire harness between the combinat ...
Weight limits
The gross trailer weight must
never exceed the TWR
described below.
Without towing package
1500 lb. (680 kg)
With towing package
3500 lb. (1590 kg)
The gross combination weight
must never exceed the
GCWR described below.
Without towing package
Vehicles without Dynamic Torque
Vectoring AWD ...